Capstan actuators can significantly lower the barrier to entry for robotics education, empowering students and makers to explore technologies that were previously too expensive to build themselves.
Any useful project in robotics requires precision control. This is what allows robots to move to the positions that you tell them to go. Without this, you can’t solve many problems. Traditional precision gearboxes such as harmonic or cycloidal drives can easily cost $500–$2000 each, placing them well outside the accessible price range for almost all makers and most schools — especially if they want students to build projects on their own or in small groups. If kids are going to solve useful problems through their tinkering, they need to have access to cheap and useful actuators.
The Capstan Drive
The capstan drive offers a cheap, and performative alternative to traditional solutions. The word “Capstan” comes from a nautical device used on ships to multiply the pulling force of sailors when hauling ropes and cables. In the world of robotics, the same principles apply, only this time, the rope serves to replace gears, in a zero-backlash, highly efficient actuator. (1)

The simplicity of the capstan drive allows for low cost and high utility in robotic applications. Due to the use of lightweight ropes and optionally 3D-printed components, the capstan drive exhibits low inertia, high back-drivability, torque transparency, and quiet operation.
High back-drivability refers to the ease with which you can drive the input by applying a force on the output. Torque transparency means there’s minimal difference in perceived force between the input and output shafts when accounting for gear reduction. For instance, in an ideal system with a 5:1 reduction, a 5 Nm (Newton-meter) torque on the output would correspond to a 1 Nm torque on the input, allowing for accurate force measurement and feedback. Additionally, capstan drives have minimal backlash — the play between moving components — which enhances control over your robot.
How Do They Work?
As briefly described before, capstan drives work because of a clever equation that says that the friction between a rope and a drum increases exponentially as you wrap the rope around the drum.
For example, if you wrap a rope around a drum five times with a coefficient of friction of 0.5 and apply a small holding force of 1 kg, the friction between the drum and the rope could hold up to 153,552,935 kg. That is about 23,000 elephants or 800 large blue whales — a tremendous amount of friction.
Given this neat fact about friction, if you wrap a rope around a small drum, then secure it to both sides of a larger drum, then tension the rope, the friction between the rope and the small drum will force the rope to pull on the large drum when the small drum is turned. this provides smooth, and zero backlash torque transmission.
Material Selection
When choosing materials for your capstan drives, you need to consider a few factors — the first being the rope. Every rope has a property known as ‘creep rate,’ which is the rate at which the rope will stretch under tension. Most synthetic ropes will creep and weaken significantly over time. When used in an actuator, this means a loss of strength and precision simply by sitting under tension. This rules out most synthetic options. What about steel cables? They are incredibly strong and durable. However, there is one serious flaw with steel cables when applied to capstan drives: they snap. When metal is wrapped around a small diameter, it is constantly bending and flexing. This repetitive movement causes strain in the material, eventually leading it to break — the same effect you get when you bend a paper clip back and forth until it breaks.
D/d Ratios
A D/d ratio is the ratio between the pulley diameter and the rope diameter.
In engineering, this ratio describes the relationship between the diameter of a cable (d) and the diameter of the shaft or pin (D) that it wraps around. For steel, you need at least a 15:1 ratio, in order to prevent significant strength loss and wear. If you were to implement this into your capstan design, it would be far too bulky. This leads us to a new type of synthetic rope that is perfect for a capstan drive.
Dynemma DM20 Rope
Unveiled in 2012, Dyneema DM20 rope has remarkable properties. It is made with an HMPE (high-modulus polyethylene) core, which eliminates creep completely under tension. This rope maintains exceptional length stability under tension for millions of cycles over many years. It is also 10 times lighter than steel while matching the strength of steel cable, making DM20 the obvious choice for a rope-based actuator.
3D-Printed Parts
If you are looking for cheap actuators, 3D printing is the obvious path. If you are clever, you can match the performance of metal parts by supporting your structural components with embedded bolts and rods. This significantly increases the strength and performance of your parts while minimizing cost.
Characteristics of Capstan Drives
Limited Rotation
Capstan drives have a couple of limiting factors, the most obvious being limited rotation. For quadruped robots or certain linkage or arm designs, this is not a problem. However, if your actuator requires continuous rotation, a different design might be preferable.
The weakness of 3D-Printed Parts
When 3D-printing components, it is important to consider the stresses involved. When coiling the rope, ensure that the rope exits on the side closest to the output drum. This reduces stress on the input shaft. It is also recommended to support the input shaft by embedding bolts or rods along its length, optionally using epoxy to increase the strength and rigidity of the component.
Limited Gear Reduction
Another important characteristic of capstan drives is their limited gear reduction. This is beneficial for qualities like torque transparency and backdrivabillity but not ideal if you need a very high reduction. You can still achieve a high reduction with more stages. For example, adding a 4:1 belt reducer between your motor and your 8:1 capstan could provide a 32:1 overall reduction. This adds complexity and mass, therefore you should consider the tradeoff before committing to a design in your own projects.
Stanley
An excellent example of capstan actuators in action is ‘Stanley,’ a quadruped robot dog developed by Ahead Robotics (ahead.io). Stanley employs capstan drives to achieve force feedback, silent operation, and reduced complexity and cost. By integrating 12 capstan-driven actuators, the robot demonstrates how this technology enables precise movement while making advanced robotics more accessible to hobbyists and students.
Stanley uses 12 capstan-driven actuators to move his legs. Notice how quiet it is when he jumps.
The creators of Stanley at described the benefits of using capstan drives as follows:
“The use of capstan drives allowed us to lower the price of the entire build. Two fabrication techniques are being used — FDM 3D printing which almost every maker now has access to, and 2D milling in FR4 — which is less available, but it is cheap to order these parts in a local shop.”
Capstan drives are a fantastic choice for hobbyists and students who are looking for a cheap, and precise alternative to traditional gearboxes.
What Can You Build?
One of the most simple uses for precision actuators is a 5-bar linkage.
Here, a capstan-driven five-bar linkage made by Aaed Musa, accurately traces the end effector through any two-dimensional path. This can be used for simple pick and place tasks, 3D printing, or quadruped legs.
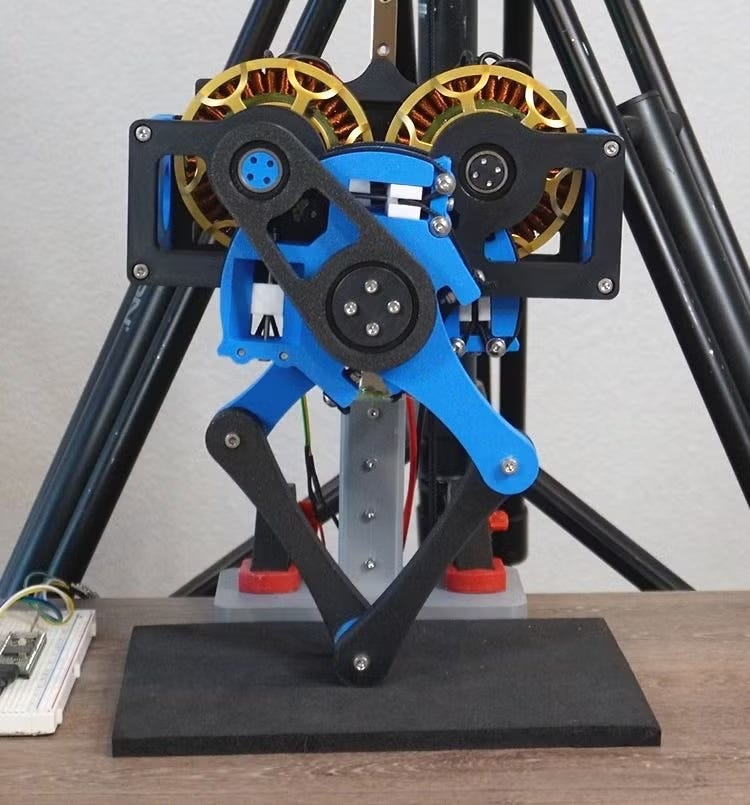
This linkage mechanism is used in projects such as the Stanford Doggo, which is a low cost quadruped robot, designed specifically with the intention of lowering the cost of valuable research platforms.
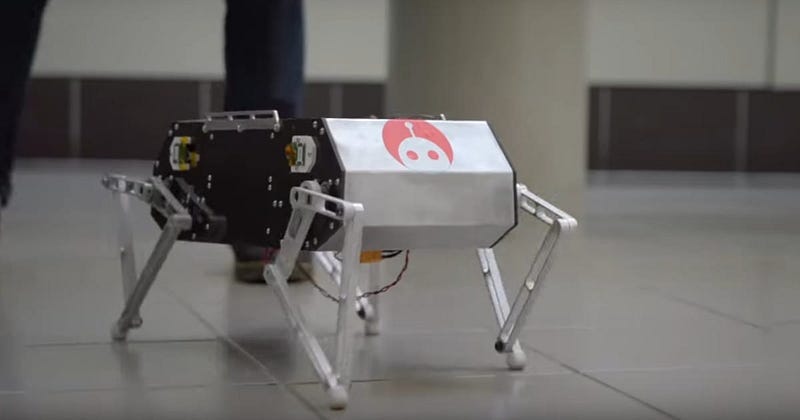
With the use of novel actuators, students can develop advanced robots at a low cost. 3D printing components to quickly iterate while reducing expenses is an incredibly powerful development strategy used by many makers nowadays.
Apart from the incredible work being done by talented students and creatives, millions of children around the world remain disconnected from the open-source communities that have made projects like this possible. When given the right tools, kids have an innate ability to learn anything. It’s essential that we nurture this natural curiosity, rather than stifling it with a rigid, one-size-fits-all curriculum.
Capstan Drives Won’t Solve Everything.
Although it may be tempting to believe that innovative, low-cost actuators will solve the toughest challenges in education, meaningful improvement requires the education system to embrace project-centered learning. This means offering more resources for student-specific projects and limiting spending on overpriced, ‘educational’ 3D printers (costing around $1,300) when that money could be spent on newer, higher-performing, and cheaper alternatives (as low as $340).
The best way to learn is to learn by doing, and it only matters if you are doing something by choice. There are thousands of open-source projects online, documented with the intention of allowing anybody to recreate them. Most of these projects are designed to be cheap, and 3D-printable. The technology already exists. The cheap actuators, clever mechanisms, and open-source software are all up for grabs. Kids simply need to be guided in the right direction. So long as schools continue to spend money on the wrong things, kids who want to build cool things are unable to.
If you are reading this article, you likely know how vibrant the open-source community is, and how instrumental 3D printing can be. In that case, I would encourage you to help the young, ambitious people around you to explore ways that they can test their creativity outside of school, leveraging the endless information that they access to.
Education is a problem that needs to be solved on a individual level. If we take action, we can help give the new generation the information necessary for them to thrive. Just imagine if every young, ambitious kid could build Stanley if they wanted to — what type of world would we be living in?
This is the vision that open source robotics provides. A generation of makers, all tinkering to solve problems and advance technology without permission from anyone.
Together, we can build this future.
Sources:
Capstan Equation:
https://en.wikipedia.org/wiki/Capstan_equation
DM20 Rope:
https://dynamica-ropes.com/products/dm20/
Stanley, the robot dog:
https://hackaday.io/project/176726-stanley-the-capstan-based-quadruped-kit
Stanford Doggo:
https://arxiv.org/abs/1905.04254 & https://github.com/Nate711/StanfordDoggoProject
Aaed Musa Capstan Drive: https://www.aaedmusa.com/projects/capstandrive &
Papers:
(1) Mazumdar, Anirban et al. “Synthetic Fiber Capstan Drives for Highly Efficient, Torque Controlled, Robotic Applications.” IEEE Robotics and Automation Letters 2 (2017): 554–561.
(2) Mazumdar, Anirban, Spencer, Steven James, Hobart, Clinton, Dabling, Jeffrey, Blada, Timothy, Dullea, Kevin, Kuehl, Michael, and Buerger, Stephen P. Synthetic Fiber Capstan Drives for Highly Efficient, Torque Controlled, Robotic Applications. United States: N. p., 2017. Web. doi:10.1109/LRA.2016.2646259.
I know someone who was paid to write technical articles for engineering magazines. You’d be great at that!! Good writing sir